What is PTH assembly in flex PCB?
- Flex Plus Tech team
- Sep 19, 2024
- 3 min read
Updated: Dec 22, 2024
In recent years, electronic products have grown more complex. They are now an essential part of people's lives. Although the performance of electronic products is constantly improving, there are still only two common methods for soldering electronic components together to form circuits: surface mount technology and plated through holes. Both SMT and PTH describe the way electronic components (such as capacitors, resistors, and microchips) are soldered to printed circuit boards. SMT and PTH soldering methods each have their own advantages and disadvantages. Since we have talked about what SMT is and its advantages and disadvantages, let's focus on what PTH is and its characteristics.
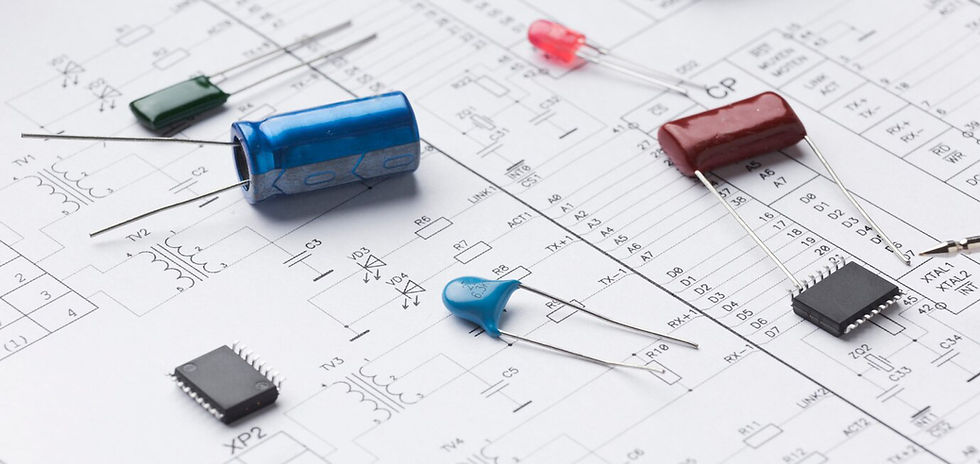
What is PTH in flex PCB assembly?
PTH is a traditional and reliable circuit board connection technology that still plays an important role in many applications. PTH is a process used to make electrical connections between different layers of a circuit board. In flex PCB manufacturing, the conduction between the surface layer and the inner layer of the circuit board is achieved by drilling holes in the PCB and then using chemical copper plating and electroplating processes to form a uniform conductive copper layer on the hole wall.
Main features:
Connection function: PTH connects each layer of circuits to ensure electrical connection.
Mounting components: Commonly used to mount through-hole components (such as electrolytic capacitors, connectors, and transistors), the pins of these components pass through the PCB, connect to the conductive pattern of the PCB through PTH, and are fixed by soldering.
Strong mechanical strength: PTH provides strong mechanical fixation, especially suitable for environments with high mechanical stress.
Characteristics of PTH components
PTH components are electronic components designed to be mounted through plated holes on the PCB. The pins of these components pass through the holes of the circuit board and are fixed on the other side of the PCB by soldering. PTH components are the most common type of components for manual soldering.

Advantages:
Strength and durability: Suitable for environments requiring high mechanical strength. Suitable for vibration and shock environments
Easy maintenance: Easy to manually solder and replace, the assembly of PTH components requires more labor. Therefore, it is not very suitable for mass production. Especially suitable for debugging and testing stages.
Current carrying capacity: Suitable for high-power applications, such as large connectors or large and heavy components (transformers, inductors, large capacitors).
Traditional design compatibility: Suitable for traditional PCB designs that require multi-layer circuit boards and complex connections. PTH components are relatively simple to hand-assemble into a PCB, so they are ideal for anyone prototyping small circuits. They can be used on breadboards and do not require soldering.
Disadvantages:
Space occupation: Need to drill holes in the PCB, which takes up more space and limits the compactness of the layout. They are also larger than SMT components, so they are not very suitable for small circuits. Due to their increasing unpopularity, many new chips do not use PTH packages.
Manufacturing cost: The manufacturing process involves drilling and copper plating steps, which are costly.
Design limitations: Design flexibility and density are not as good as SMD.
Application scenarios of PTH components
High-power applications: such as power supply modules and power amplifiers.
Industrial and automotive electronics: Provide high mechanical strength and reliability.
Traditional circuit board design: Suitable for multi-layer circuit boards and complex electrical connections.
Differences between PTH components and SMD components

1. Pins and mounting methods
PTH components have longer pins. The pins pass through the PCB and are soldered on the other side, forming a noticeable pin protrusion.
SMD components are directly attached to the PCB surface without perforation, and the pins or contacts are short and flat on the PCB. The appearance is flat and there are no protrusions.
2. Physical characteristics
PTH components: Larger in size, with more visible pins and body. Tall and prominent in shape.
SMD components: Small and flat, suitable for high-density layout. Flat in shape, flush with the PCB surface.
3. Soldering points and pads
PTH components: Pins pass through the PCB through holes, with soldering points visible on both sides. There are pads on the inside of the holes to connect and fix the pins.
SMD components: Soldering points are on the surface of the PCB, in direct contact with the bottom of the component.
These differences in appearance help distinguish these two different types of electronic components during design and production. Generally speaking, PTH components are larger than SMT components, making them less suitable for the shrinking world of consumer electronics.
With this knowledge, you will have a clear idea of which components you should choose for your circuit board. Flex Plus specializes in providing a variety of flexible PCB assembly solutions. With professional knowledge and advanced manufacturing technology, we provide high-quality flexible circuit board products and customized solutions to meet your specific needs.
Comments