What is Flexible PCB Heater?
- Flex Plus Tech team
- Sep 23, 2024
- 5 min read
Updated: Jan 7
Flexible PCB heater is a heating element based on PI film. It has excellent high-temperature resistance, corrosion resistance, and insulation performance and is widely used in the heating needs of various devices. Its working principle is that the circuit pattern on the PI film generates heat when powered on. Flexible PCB heater has broad application prospects, especially for modern electronic devices and wearable technology. Thanks to its flexible structure, lightweight, good conductivity, and bending resistance, it can be well adapted to curved or irregular surfaces and can be made into square, round, and other shapes of heaters. Compared with traditional electric heaters, flexible printed circuit heaters have shown strong advantages.

Main components of a flexible PCB heater
1. PI film substrate
As the base material of the flexible PCB heater, PI film provides excellent insulation performance and high-temperature resistance. PI film has good flexibility and corrosion resistance and can work in extreme environments. It can usually withstand temperatures up to 300°C, and its thickness is usually between 0.05 mm and 0.2 mm, which is suitable for applications with complex curved surfaces and narrow spaces.
2. Heating resistor materials
Heating resistor materials mainly use metal foils (such as copper foil, nickel foil, aluminum foil) or metal resistance wires (such as nickel-chromium alloy, nickel-aluminum alloy), which have good conductivity and stable resistance characteristics. The resistor material generates heat after being energized, and the resistor material determines the heating effect of the heater. The heating pattern is usually engraved into a circuit pattern by etching technology to ensure uniform heating and achieve customized heating needs.
3. Insulating layer
Covered on the heating resistor layer to ensure safety, prevent electrical short circuits, and further enhance the heat resistance of the flex PCB heater. The material is usually the same as the substrate, mostly PI film, and other insulating materials such as polyester film (PET) may also be used.
4. Conductive terminal or connecting wire
Its function is to connect the power supply and provide current to the heating resistor. The design of the circuit needs to consider conductivity and mechanical strength to ensure long-term stable operation. Usually located at one end or edge of the heater, the circuit is connected to the resistive material by welding or crimping.
Principle of Flexible PCB Heater
The working principle of the flexible PCB heater is based on the principle of converting electrical energy into thermal energy. The specific process is as follows:
Working mechanism: When the current passes through the resistor in the PI film, according to Ohm's law, the electrical energy is converted into thermal energy, causing the metal conductor to heat up rapidly. The high thermal conductivity efficiency of the PI film can quickly and evenly transfer the heat generated by the metal conductor to the heated object.
Design features: The design of the Flex PCB heater takes into account the problem of heating uniformity. By reasonably designing the pattern and layout of the heating element, the current is ensured to flow evenly in the heating area, thereby avoiding heat concentration in certain areas, which causes local overheating or uneven heating.
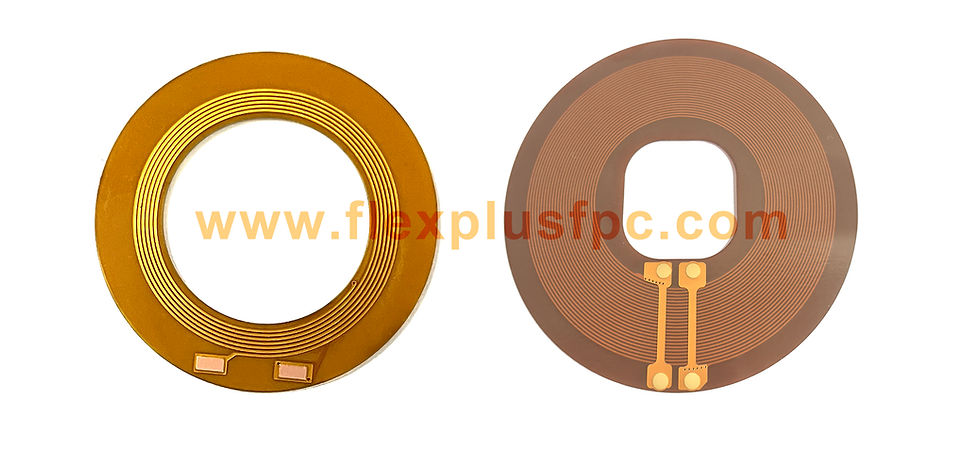
8 advantages of Flexible Circuit Heater
1. High-temperature resistance and corrosion resistance
It can work continuously at higher temperatures (usually between 200°C and 300°C), and its high-temperature resistance is excellent. It has a strong resistance to chemicals and humidity and is suitable for harsh environments.
2. Good insulation performance
PI film has strong insulation and can prevent short circuits and leakage. The insulation resistance is greater than 100 MΩ.
3. Precise heating
Flexible film heaters can heat almost anywhere needed by sticking the heater to the surface of the heated part. Flexible circuit heaters with higher heat flux density can be customized in places with large heat loss.
4. Fast preheating speed and long service life.
Flexible circuit board heaters have a larger thermal conductivity area than wound heaters. Therefore, a higher heat flux density is allowed to be generated, and heating is fast, thus extending the life of the insulation material. FPCB heaters can operate at twice the heat flux density of comparable wound heaters. The insulation life can be extended by 10 times.
5. Integrated electronic components
Electronic components such as resistance thermometers, thermostats, or thermistors can be integrated into flexible film electric heaters, which can save assembly time and costs for users.
6. Thin and flexible, it reduces weight.
Flex PCB heaters usually weigh only 0.023-0.037 g/cm², and the thickness is usually around 0.1-0.5 mm. Compared with traditional rigid circuit boards, flexible PCBs have a lighter and thinner structure, which has significant advantages in saving space and weight. Especially for miniaturized electronic products and portable devices, flex printed circuit board can adapt to complex 3D structures or curved surfaces without damaging the circuit, which makes them more widely used.
7. Efficient energy conduction
Since flexible PCBs usually use highly conductive copper foil materials, they can generate sufficient heat or magnetic fields at lower currents, which makes them more energy-efficient in heating applications.
8. Customized design
Flexible PCBs can be designed with complex patterns or heating paths according to requirements and can be customized flexibly for different heating needs.
Application scenarios
Since the PI heater has excellent insulation strength, electrical strength, thermal conductivity efficiency, and resistance stability, it is not only suitable for various industrial heating needs, but it can widely used in medical, aviation, aerospace, new energy, and other fields, providing efficient and reliable heating solutions for various application scenarios.
Consumer electronics:
Flexible heaters can be integrated into electronic devices such as smartphones and laptops to prevent equipment damage in cold environments or to achieve specific temperature control functions.
Automotive industry:
Flex PCB can be used for anti-fog and anti-freeze heating of car seats, steering wheels, on-board cameras, car rearview mirrors, wipers, diesel vehicle filters, or battery systems to provide comfort or ensure the normal operation of batteries in low-temperature environments.
Health and medical equipment:
In smart clothing or health monitoring equipment, flexible PCBs can be used as heaters to provide users with heating functions and improve the comfort of the wearer, such as smart gloves, back heating devices, etc. Flexible PCBs can also be used in medical sensors or treatment devices to provide local heating for specific parts to promote blood circulation or assist in treatment.
Aerospace:
Used in temperature control systems in satellites and aircraft, this type of heater is usually used with temperature sensors and temperature control systems to accurately control the temperature.
Industrial applications:
Used to maintain equipment temperature or heat certain specific parts, such as instruments, incubators, displays, and circuit board antifreeze.

Design and manufacturing considerations
Material selection:
Usually, copper foil or other conductive materials with high conductivity is used, and the high-temperature resistance and fatigue resistance of the material need to be considered.
Line width and line spacing design:
The design of FPCB heaters requires precise control of line width and line spacing to ensure a uniform heating effect when current passes through, and no safety problems are caused by overheating.
Thermal management:
Flexible PCBs as heating elements require good thermal management to prevent damage caused by overheating or uneven local temperatures. The uniform distribution of heat and the overall heat dissipation performance of the equipment should be considered during design.
Summary
The use of flexible PCBs as heaters is increasingly valued in various fields because of their flexibility, lightness, and high efficiency. Through electromagnetic induction or resistive heating, they play an important role in many fields such as wearable devices, medical applications, and industrial equipment. In the future, with the development of flexible electronic technology, the heating application of FPCBs will be more extensive, promoting the emergence of more innovative products.
Comentarios