The Concept of Back Bared Flexible PCB
Back Bared Flex PCB is a special type of flexible circuit board with unique structural and application advantages. In back bared flex PCB, part or all of the back side of the substrate is removed to expose the bare copper traces (conductive traces). After removing the substrate, the copper traces can be directly connected to other circuits or components, reducing contact resistance and improving the reliability of electrical connections. In the printed circuit board industry, the design of back bared flexible PCB is also known as dual access Flex PCB. Just as its name implies, these circuits have insulated openings on both the top and bottom sides, so allow the double-sided conduction of a single copper plane. The unique and critical step in creating a back bared flexible PCB solution is substrate lamination. This can help understand the subtle differences in design between single-sided and back bared flexible PCB.

The Production Process of Back Bared Flexible PCB
Back bared flexible PCB typically first laminate a customized pre-drilled or drilled dielectric film onto a single layer of copper. Imaging and etching of copper to form a copper pattern at the opening aligned with the pre-perforated dielectric film. These positions become entrances from the back. Then we apply the pre-perforated dielectric or photoimaged solder mask to the top. For surface contact and/or providing a solderable surface, additional electroplating and other surface finishing processes can be added, such as reflow soldering or electroless nickel immersion gold(ENIG).
Another increasingly popular method for creating back bared flexible printed circuit board is laser ablation of selected areas to remove dielectrics. This process requires strict control by ablating through thin films and adhesives, while leaving behind copper. This is a very precise process that can be completed with stricter resolution compared to pre drilling the dielectric film before lamination. Using expensive equipment (laser ablation) is usually a more expensive processing option.

The Main Advantages of the Back Bared Flexible PCB
We create electrical access points on the back of the circuit without the additional cost of creating double-sided circuits. Components can be inserted and welded from both the top and bottom sides. The exposed area can be a pad or a trace spanning the opening. A design with similar functionality can create a double-sided circuit, but requires an additional layer of copper and polyimide film as it is an extra copper plating process.
Creating exposed copper "fingers" that are directly soldered from one rigid circuit board to another in jumper cables. This is a highly reliable and low-profile method to replace connectors, commonly known as sculptural circuits. Usually, exposed fingers need to be thicker than other parts of the circuit. Exposed insertion refers to the process of etching differently to create circuits with variable copper thickness, where the pin features are bent to match the contour of the inserted connector.
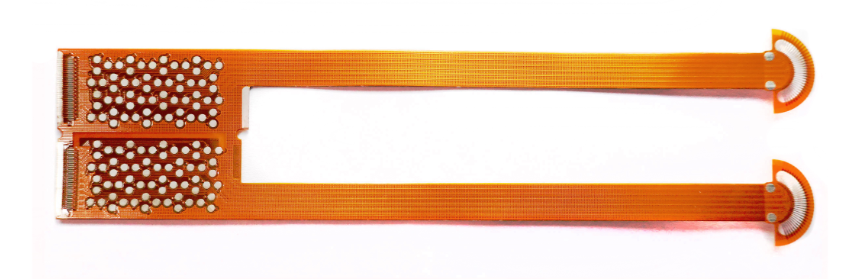
As a special type of flexible circuit board, back bared Flex PCB has shown broad application prospects in many fields, especially in the aerospace industry, due to its unique structural design and significant advantages. Understanding and applying this circuit board will help engineers and designers achieve more breakthroughs in electronic product design.
By focusing on controlling shrinkage through film material management, there is exposure process expertise, copper plating precision, and outline punching excellence. Flex Plus delivers FPCBs of unparalleled quality, reliability, and dimensional accuracy. Their commitment to excellence stands as a testament to their unwavering dedication to surpassing industry norms and providing customers with top-tier FPCB solutions. When quality is non-negotiable and precision is paramount, Flex Plus emerges as the undisputed choice in FPCB manufacturing, setting a new benchmark for quality in the competitive landscape of Chinese FPCB factories.
Comments