What are the applications of Flexible printed circuit in automotive ?
- Flex Plus Tech team
- Jun 11, 2024
- 4 min read
Updated: Mar 12
For cars, both fuel vehicles and electric vehicles need to use Flexible printed circuits. In an automotive, up to 100 Flexible printed circuits may be used. Many automotive PCB applications involve sensors, cameras, radars, and other electronic devices in modern cars that need to be connected by Flexible printed circuits, which can withstand the challenges of the external environment of the car, such as temperature changes, humidity, vibration, etc., and ensure the stable operation of electronic equipment. In addition, Flexible printed circuits can also be used in the lighting system of the car, such as headlights, instrument lights, etc. Because it has excellent conductivity and flexibility, it can meet the complex line layout and curved surface design requirements of headlights and improve the design freedom and reliability of headlights.

Development trend of Flex PCB technology in automotive
Flex PCB technology was first introduced in 1950. Today, it is not a new technology, but its application in the automotive field is gradually becoming popular, just like other traditional technologies crossing over to the automotive field. The growing interest in this technology highlights the rapid expansion of the automotive FPC market. It will be very smooth to use Flex PCB technology in automobiles. The wiring harness system of traditional automobiles is complex and messy, and multiple interfaces bring complex and high costs to the vehicle's electronic system. In the era of smart cars, the algorithm capabilities of vehicle computers have far exceeded the current connection technology, so the change of carriers is only a matter of time.
Core application of Flexible printed circuit in automotive lights
In automotive lights, Flex plus FPC brings more possibilities to lighting design, improves functionality and performance, and makes automotive lights more intelligent and personalized. The application of Flex PCBs in automotive lights has the advantages of flexibility, bendability, and easy wiring, which can meet the requirements of flexibility and reliability in automotive light design. At the same time, through the Flex PCBs application, the integration and design freedom of automotive lights can be improved, and more diverse lighting effects and functions can be achieved. Flexible printed circuits are mainly used to connect and drive various electronic components in lamps to realize the functions of lighting on and off, dimming, and flashing. These advancements highlight the importance of automotive PCB applications, which encompass not only lighting systems but also a wide range of electronic functionalities within vehicles. FPC board can adapt to complex design requirements and ensure stable operation. They have high space utilization, strong reliability, strong anti-interference ability, and high-temperature resistance.

Lamp bead connection:
FPCB can connect LED lamp beads with driver circuit boards to realize power supply and control signal transmission of LED lamp beads. The flexible characteristics of Flexible printed circuits allow it to adapt to complex lamp shapes and simplify the layout of connection lines.
Light strip connection:
The commonly used light strips in automotive lights (such as daytime running lights, brake lights, turn signals, etc.) can also be connected to the driver circuit board through flexible PCB to realize power supply and control of the light strips. The flexibility and bendability of a flexible printed circuit enable it to adapt to the curves or curved shapes of the light strips.
Light control module connection:
The control modules in automotive lights usually include light switches, dimmers, flashing controllers, etc. FPCBs can be used to connect these modules with lamps to realize functions such as control, adjustment, and flashing of lights.
Signal transmission:
Flexible PCBs can also be used to transmit vehicle signals, such as brake signals, turn signals, etc., and transmit these signals to the driver circuit board of the automotive lights to realize the corresponding response of the automotive lights.
Advantages of Flexible PCB in Automotive Lights
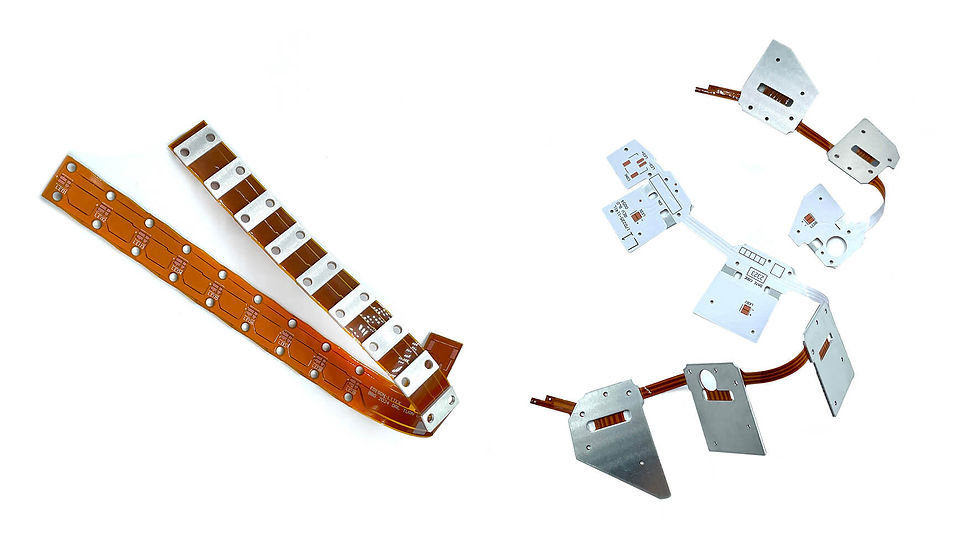
Improve design flexibility and adaptability
FPCB in automotive lights have excellent flexibility and can adapt to various complex design requirements, providing electric vehicles with richer functions and higher performance.
Save energy and achieve lightweight
The lightweight design of FPCB helps to reduce the overall weight of electric vehicles, improve energy efficiency, and extend the driving range.
Enhance durability and reliability
Flexible printed circuits for automotive lights reduce connection points, improve the stability and durability of electrical connections, and extend the service life of components.
Optimize heat dissipation performance
Flexible printed circuits have better heat dissipation performance than traditional rigid circuit boards, which helps to improve the overall performance and safety of electric vehicles.
Practical application cases of Flexible PCB in electric vehicles
Many mainstream electric vehicle brands (such as Tesla, NIO, and BYD) have adopted Flexible printed circuits. User feedback shows that vehicles using Flexible printed circuits have excellent performance in lighting effects, operational feedback, and overall performance, which improves driving satisfaction.
With the electrification and intelligent development of the automotive industry, Flex PCB has been increasingly used in automotive PCB applications due to its advantages, such as excellent bendability, lightweight design, and high automation level. Flex Plus FPC is widely used in scenarios such as automotive lights, display modules, the three major power control systems of BMS/VCU/MCU, sensors, and advanced assistance systems. The rapid development of the new energy vehicle market has promoted the surge in demand for Flexible printed circuits for automotive power batteries.
Comments