Rigid-flex PCB, Flex-rigid circuit board
- Flex Plus Tech team
- Aug 12, 2024
- 4 min read
Updated: Mar 11
The above is a Rigid-flex PCB, and it represents quite the leap forward in PCB technology as they are needed to be both flexible yet stiff for today's versatile electronics. Because the requirement for a smaller, more reliable electronic component is in demand and gaining traction everywhere, the Rigid-flex circuit has gained exposure across different industries. In this detailed guide, let’s take a look at what Rigid-flex circuit boards are, their advantages and disadvantages, and the manufacturing process.

1. What is Rigid-flex PCB?
Definition and Structure
Rigid-flex PCB is made by combining a rigid circuit board with a flex circuit board. The rigid part is used to place components and support, and the flexible part can be bent to connect different rigid parts. This design of the circuit board has both rigid strength and flexibility.
Rigid PCB Vs Rigid-Flex PCB
Whereas traditional rigid circuit boards are inflexible, Rigid-flex circuit boards combine the benefits of both flexibility and fortitude. This is good for applications that have a small form factor with an immense level of reliability. It means they eliminate more connectors and interconnects, reducing the number of failure points to give a tougher performance.
Working with an expert in Rigid-flex PCB manufacturing is the only way to maximize everything these hybrid circuits have to offer your product designs.
2. Major Design Challenges of Rigid-Flex PCBs
Common Design Issues
Creating these types of PCB boards has its own set of complications, from avoiding mechanical stresses on the flex portions to maintaining a physical connection between them and any rigid areas. Design challenges Thermal management, impedance control signal integrity issues
Design Considerations
Designers need to stress significant bend radius that is compliant with the bendable part, components placement, and general layout on PCB in order to tackle these challenges. Also, it is very important to work closely with the manufacturer of Rigid-flex circuits so that the PCB required in this template is made on time and reliably.
3. Rigid-flex PCB Manufacturing Materials
Common Materials
PI is often used in bendable layers, while FR4 can be found in the rigid sections; there are also several adhesives that bond these layers. The materials that are used to make circuit boards affect not only the flexibility of a board but also its thermal and long-term performance.
Material Selection Criteria
Selecting the right material is often a trade-off between properties such as flexibility and heat resistance. The material selected must match the capabilities of the specific manufacturing process and must also meet the performance specifications required for each specific application.
4. Manufacturing Process of Rigid-Flex PCBs
Flex-Rigid PCBs combine the best of both worlds while enjoying unparalleled advantages, but their manufacture requires several key steps that require absolute precision and attention to detail.
Design and Layout: It all starts with designing the circuit board layout, considering each kind of requirement for both rigid and flexible sections.
Material Selection: It is very important to choose the material wisely as this will directly affect the performance and reliability of the Rigid-flexible PCB. It is choosing the right substrate for both the rigid and flexible layers.
Lamination: The compliant layers are laminated onto the rigid parts by a bonding process to assure good adhesion without hindering its flexibility.
Drilling and Plating: Drill holes to create via; Holes are plated with copper to create a conductive.
Photo Etching: The copper is photo-etched to create the desired traces on both the rigid and flexible portions of your design.
Assembly & Testing: In this stage, components are assembled on the PCB formed by earlier stages and then tested for reliability.
5. Is Rigid-flex PCB reliable?
The answer is yes; the reliability of Flex-rigid PCB is unmatched. Because they can withstand mechanical stress, vibration, and harsh environments, they are ideal for industries such as aerospace, medical devices, and military electronics. In other words, in complex applications that cannot be achieved with rigid PCBs, Rigid-flex PCBs provide a perfect solution.
It is widely used in compact, lightweight, functional design devices for applications with higher reliability requirements. For example, foldable screen mobile phones, smart monitoring bracelets, etc. In this case, it is crucial that the circuit board can bend without damaging itself. In addition, the use of Rigid-flex circuits also eliminates and reduces the installation of multiple connectors and cables, thereby improving the reliability of the overall service life.
6. Pros and Cons of Rigid-Flex PCBs
Advantages
Design Flexibility: The use of Rigid-flex circuits allows for more complex circuit designs, enabling engineers to make circuits that conform to irregular shapes or fold into smaller spaces.
Compact Design: The combination of flexible and rigid components significantly reduces the overall size of the circuit board, making it suitable for compact devices.
Increased Durability: Compared to rigid PCBs, its flexible layer can absorb mechanical stress, thus preventing further damage.
Fewer Connects: Few connectors and interconnect issues are a reliability issue for your circuit board design. Increasing the number of connections increases the odds that something will fail in this area.
Disadvantages
Increased Manufacturing Costs: The complexity of Rigid-flex PCBs can result in higher production costs compared to Rigid PCBs or flexible PCBs. These include unique materials and production processes.
Complexity: The added complexity of the design complicates the design process by determining the mechanical and electrical characteristics of both the rigid and flexible parts.
Longer Lead Times: The manufacturing of Rigid-flex printed circuits is a complex process, so the lead times are longer than for Rigid circuit boards.
Flex Plus Case:
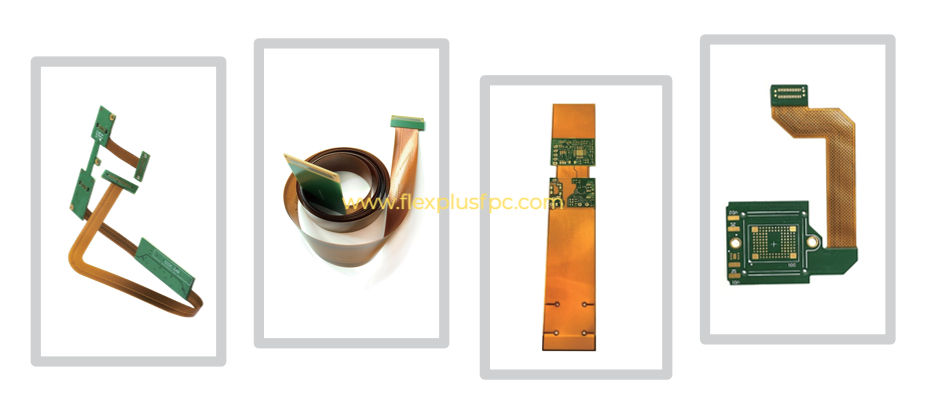
Conclusion
The flexibility and reliability of Rigid-flex circuits make them an essential element in today's electronic layouts. Therefore, whether you are designing a small, lightweight consumer product or a critical aerospace workhorse, you should not overlook the capabilities and challenges of Rigid-flex PCBs. Partner with a proven Flex-rigid PCB manufacturer, and your product will have the best performance, reliability, and performance.
Comentarios