Polyimide Flex PCB: The Ultimate Guide
- Flex Plus Tech team
- Mar 25
- 4 min read
Updated: Mar 31
Why Polyimide Flex PCBs Are Becoming Essential in Modern Electronics
Polyimide PCBs have become a staple in the modern electronics world due to their unparalleled flexibility, durability, and performance in rugged applications. With the potential for more versatility to exploit, polyimide-based PCB is already reshaping what is expected at the end of the line for engineers, designers, and manufacturers alike. This article discusses the characteristics, types, benefits, and edge polyimide flex PCBs have over potions such as FR4.
What is Polyimide PCB?
Thermal stability, mechanical strength, and chemical resistance are features of polyimide PCB; Polyimide is a high-performing polymer. Polyimide flex PCBs differ from rigid PCBs in that they can bend, twist, and fold without compromising their electrical performance. This renders them appropriate for utilizations that include development constraints or complex geometries.
Polyimide usually comes as a substrate bonded to copper trace lines, which are used to form electrical connections. Such materials’ resistance to temperature and environment extremes in excess of 400°C makes them stand out from regular PCB materials, which is why these materials are widely used in the aerospace industry, medical instruments, automotive electronics, and consumer electronics.
Types of Polyimide Flex PCBs
Polyimide flex PCBs come in different types, depending on their structure and use:
1. Single-Sided Polyimide Flex PCB: It has one copper layer on one side of the polyimide material.
Simple and cost-effective, it is commonly used in basic electronic devices.
2. Double-Sided Polyimide Flex PCB: It has copper layers on both sides, connected by small holes called vias. Used in more complex circuits that need more connections and components.
3. Multi-Layer Polyimide Flex PCB: It has three or more copper layers, making it more advanced. Commonly found in high-performance devices that require compact and efficient circuit designs.
4. Rigid-Flex PCB: Combines a stiff (FR4) layer with a flexible polyimide layer. Used in devices that need both flexibility and solid support, such as medical instruments and aerospace systems.
Advantages of Polyimide PCB
Polyimide flex PCBs offer a range of benefits that make them indispensable in modern engineering:
Thermal Stability: Polyimide can endure extreme temperatures without degrading, making it perfect for high-heat environments like engines or industrial machinery.
Flexibility: The material’s pliability allows it to fit into tight spaces or adapt to moving parts, reducing the need for connectors and improving reliability.
Lightweight: Compared to rigid boards, polyimide PCB is significantly lighter, a critical factor in aerospace and portable electronics.
Durability: Resistant to chemicals, moisture, and mechanical stress, polyimide ensures long-term performance in harsh conditions.
High Dielectric Strength: Its excellent insulation properties support reliable signal transmission, even in compact designs.
Why Use Polyimide for Flexible PCBs?
Because of the unique combined properties of polyimide flexible PCB, people choose it. Flexibility is the main core factor, and unlike rigid materials, polyimides can conform to 3D shapes or bend during operation, thus reducing the complexity of assembly. Its heat resistance also makes it ideal for environments where welding processes and heat dissipation are a challenge. In addition, the fatigue resistance of polyimides ensures that PCBs remains conductive lines intact even after repeated bending, a key requirement for wearable technology, foldable displays, and robotics.
From a design point of view, polyimides can be miniaturized without sacrificing performance. As devices shrink, the need for lightweight, flexible, and reliable circuits grows, and polyimides meet these needs.
Factors to Consider When Choosing Polyimide PCB
When selecting a polyimide flex PCB, keep these factors in mind:
1. The application needs to consider how often the PCB will bend, the temperature it will face, and the environment it will be used.
2. Cost Polyimide is more expensive than materials like FR4, so make sure it fits your budget.
3. Thickness polyimide PCBs come in various thicknesses (e.g., 25 μm to 125 μm). Thinner flex PCBs are more flexible, but they may be less durable.
4. Number of Layers decide how many layers you need based on your circuit complexity and available space.
5. Manufacturing expertise make sure to choose a trusted supplier with experience in polyimide PCB production, as precision and expertise are required for flex PCB manufacturing.
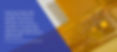
What is FR4 PCB Material?
FR4 (Flame Retardant) is a widely used rigid PCB material made from woven fiberglass cloth impregnated with an epoxy resin. Indicating its compliance with safety standards. FR4 is known for its affordability, rigidity, and decent thermal and electrical properties, making it the standard choice for traditional electronics like computers, TVs, and household appliances. However, it lacks the flexibility and high-temperature tolerance of polyimide.
Why Choose Polyimide Over FR4?
Choosing polyimide or FR4 depends on the specific needs of your project.
Feature | Polyimide Flex PCB | FR4 PCB |
Flexibility | Can bend and move | Stiff and cannot flex |
Heat Resistance | Withstands 400°C | Typically up to 130°C |
Weight | Lightweight | Heavier |
Durability | Resists chemicals and bending | Can crack under stress |
Cost | More expensive but high-performance | More affordable for simple projects |
Polyimide is renowned for its exceptional thermal stability, making it a top choice for high-temperature applications. Here’s a detailed breakdown of its temperature resistance:
1. Standard Operating Range
Short-term exposure: Up to 400°C (752°F) without significant degradation.
Continuous use: Typically -269°C to +260°C (-452°F to +500°F), depending on the specific polyimide grade (e.g., Kapton® HN can withstand 260°C long-term).
2. Key Temperature Benchmarks
Glass Transition Temperature (Tg): -250~400°C (varies by formulation).
Melting Point: Polyimide does not melt but decomposes at >500°C (932°F).
Cryogenic Performance: Remains flexible and functional even at -269°C (near absolute zero).
If your design needs flexibility, heat resistance, or durability, polyimide PCB is the best choice. If your project requires a simple, cost-effective rigid PCB, FR4 is a better option.
Conclusion
Polyimide flex PCBs represent a leap forward in printed circuit board technology, blending flexibility, resilience, and performance into a single package. Whether you’re designing cutting-edge wearables, aerospace components, or medical devices, polyimide offers unparalleled advantages over traditional materials like FR4. By understanding its types, benefits, and key selection factors, you can make informed decisions to optimize your next project. For applications demanding adaptability and durability, polyimide stands as the superior choice, paving the way for innovation in an increasingly compact and complex world.