Main Types of Flex PCB Solder Mask
- Flex Plus Tech team
- 4 days ago
- 2 min read
Flex PCB solder mask stands as a critical element in flexible printed circuit boards, directly impacting reliability, durability, and manufacturability. The selection of a flex PCB solder mask type proves essential for optimizing performance in dynamic flexing or densely packed circuit environments.
This article examines how flex PCB solder mask functions, its importance in flexible circuit design, and the primary variants employed in modern manufacturing processes.
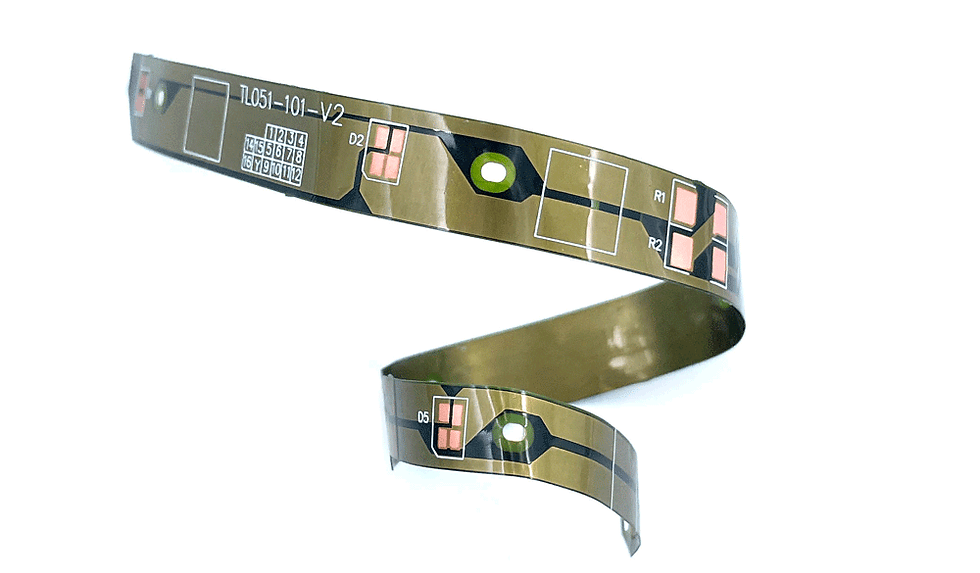
What Is a Solder Mask and Why Is It Important?
A solder mask (also known as solder resist) is a protective polymer coating applied to the surface of a printed circuit board. Its primary function is to:
Prevent solder bridging between conductive traces during assembly.
Protect copper traces from oxidation and environmental contaminants.
Improve insulation resistance and long-term circuit integrity.
Enhance aesthetics and solderability for final products.
For flex PCBs, the solder mask must also accommodate mechanical bending, thermal cycles, and space constraints, making the selection more critical than in rigid boards.
Main Types of Flex PCB Solder Mask
There are several types of solder masks suitable for flexible PCB applications. Each type has unique characteristics in terms of flexibility, adhesion, and process compatibility.
1. Screen-Printed Liquid Photoimageable (LPI) Solder Mask
This is one of the most common types used in both rigid and flexible PCBs.
Key Features:
Excellent resolution for fine-pitch components
UV curable after image development
Offers good chemical resistance and durability
Pros for Flex PCBs:
Cost-effective
Customizable thickness
Compatible with complex designs
Limitations:
May not be ideal for areas requiring high flex cycles
Requires flat surfaces for proper adhesion
2. Flexible Coverlay (Polyimide Film + Adhesive)
While not a solder mask in the traditional sense, coverlay is widely used as a solder resist layer in flex PCB manufacturing.
Key Features:
Made of polyimide film laminated with adhesive
Highly flexible and durable
Excellent mechanical strength
Pros:
Superior flexibility for dynamic applications
Better resistance to cracking during bending
Ideal for wearable and foldable electronics
Limitations:
Higher cost than LPI
More complex lamination process
3. Photo-Imageable Coverlay (PIC)
A hybrid option that combines the flexibility of coverlay with the precision of photoimageable materials.
Key Features:
UV curable, similar to LPI
More flexible than standard LPI solder masks
Can be laser-drilled or photodefined for fine features
Pros:
Excellent for fine-pitch SMT components
Flexible and dimensionally stable
Simplifies manufacturing over traditional overlay
Limitations:
Newer technology, may be limited in supplier availability
Requires controlled exposure and curing conditions
How to Choose the Right Solder Mask for Flex PCBs?
When selecting a flex PCB solder mask, consider the following:
Flexibility Requirements: Dynamic vs. static flex applications
Board Thickness & Design Density: Thinner boards may benefit from PIC or coverlay
Thermal & Chemical Resistance Needs
Cost Constraints
Assembly Method Compatibility
For high-flex or wearable electronics, polyimide coverlay or photo-imageable coverlay is often the best choice. For less demanding applications, LPI solder mask may offer a good balance between cost and performance.
Summary
The type of flex PCB solder mask you choose affects how long your product lasts, how dependable it is, and how well it works. If you learn about common options like liquid photoimageable masks, polyimide films, and light-sensitive coverlays, you can pick the right material for your project’s needs.
When building flexible circuits, always ask your flex PCB manufacturer to help choose the best solder mask for your design.
Comments