Flex PCB for Glucometer Test Strip
- Flex Plus Tech team
- 6 days ago
- 2 min read
As the core consumable of blood glucose monitoring systems, the flex PCB for Glucometer Test Strip plays a crucial role in determining the accuracy of test results. With growing patient demand for portable, rapid, and low-cost diagnostics, traditional screen-printed electrodes are increasingly showing limitations such as poor stability and high manufacturing variability. In contrast, flexible printed circuits, with their advantages in miniaturization, high consistency, and signal fidelity, are reshaping the technological framework of glucose test strips. This article analyzes the critical role of flex PCB technology in test strips and explores future breakthroughs from the flexible PCB perspective.
Why Flex PCB for Glucometer Test Strip is the Ideal Solution
Blood glucose test strips must complete electrochemical analysis of glucose concentrations in blood samples within 0.5 seconds. This imposes stringent requirements on the precision, anti-interference capability, and biocompatibility of conductive pathways. Compared with traditional SPEs, flex PCBs offer the following disruptive advantages:
Micron-Level Circuit Precision
flex PCBs use photolithography processes to create fine circuits with line widths and spacing ≤50μm (whereas traditional SPEs can only achieve ≥100μm). This reduces resistance variations in signal paths and ensures consistent electrochemical responses across different test strip batches (CV value < 3%).
Multi-layer Structural Integration
By stacking 2–4 layers of flexible substrates, flex circuit boards can integrate the working electrode, reference electrode, and signal compensation circuitry within a limited area (typically <5mm²). This supports differential signal detection to eliminate environmental noise.
Biocompatible Packaging
Flex PCB surfaces can be coated with medical-grade parylene C, isolating the circuit from direct contact with blood while allowing oxygen permeability to maintain redox reaction stability.
Cost Advantage in Mass Production
Roll-to-roll production processes enable flex printed circuits to reduce the per-strip circuit cost to below $0.02—30% lower than SPE-based designs—with a yield rate improved to 99.5%.
Integrated Design of flex PCB and Test Strip Structure
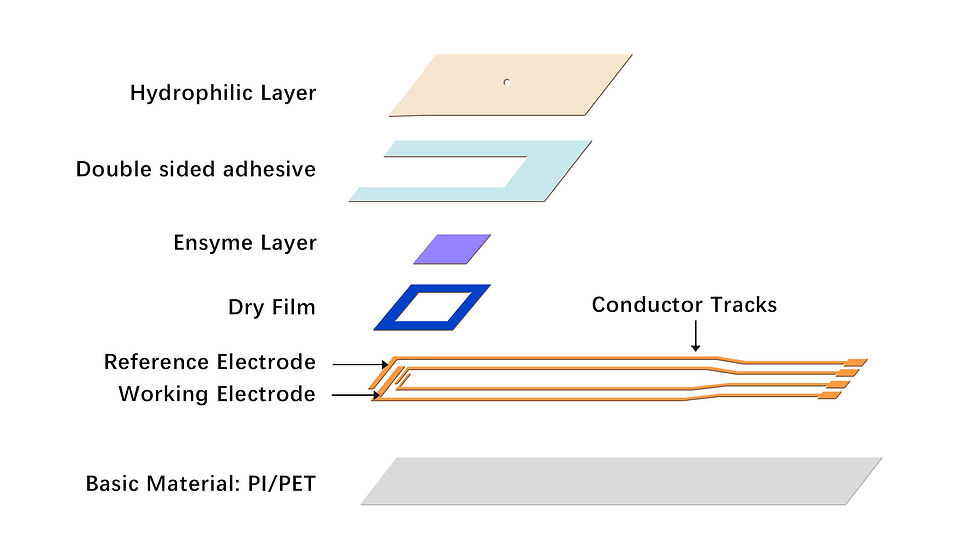
A typical flex PCB for a glucometer test strip consists of the following layers (from top to bottom):
Hydrophilic Cover Layer: Guides blood to quickly fill the detection zone.
Reaction Layer: Contains biochemical reagents like glucose oxidase and mediators (e.g., potassium ferricyanide).
Flexible PCB Electrode Layer: Integrates the working electrode, reference electrode, and counter electrode.
Insulating Substrate: Made from polyimide or liquid crystal polymer, supporting the circuit structure.
Contact Terminals: Metal contacts are connected to the glucose meter slot.
Working Principle of Flexible PCB in Glucose Test Strips
When a drop of blood is applied to the test strip, glucose reacts with enzymes (e.g., glucose oxidase), generating electrons and a weak electrical current. This current is conducted through the electrode traces on the flexible PCB. The glucose meter reads the signal, calculates glucose concentration, and displays the result. Measurement accuracy hinges on the quality of conductive traces on the flex PCB board.
Core Application Scenarios of Flex PCB in Glucose Test Strips
High-Sensitivity Electrode Array Design
Flex PCBs can be customized with electrode patterns (e.g., interdigitated, spiral) to double the effective area of the working electrode compared to traditional circular designs.
Wireless Data Tag Integration
Next-generation smart strips incorporate an NFC chip at the FPCB tail end, enabling instant upload of test data to smartphones. It also logs batch numbers and expiration dates to prevent the use of outdated strips.
Comments