Advancements and Application of Flexible Printed Circuit in EV Power Battery Modules
- Flex Plus Tech team
- Jun 28, 2024
- 4 min read
Updated: Mar 12
Around 2017, flexible printed circuits were just starting to be used in the power battery industry. Due to the initial high production costs and strict requirements for reliability in the automotive electronics industry, many power battery companies were still observing at the time. As the excellent performance of flexible printed circuit gradually appears, and the cost of large-scale production is rapidly decreasing, the process of replacing traditional wiring harnesses with flexible printed circuit is apparently accelerating. Public information shows that companies such as Tesla, Gotion High tech, Calb-tech, Tafel, Sunwoda, and Farassis Energy have started using flex PCBs. At present, flex PCB solutions have become the first choice for most new energy vehicles.
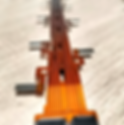
Integrating Flexible Printed Circuit Solutions in Battery Management Systems
The flexible printed circuit solution is developing towards the integration of CCS (cell connection system), combined with plastic structural components, copper and aluminum bars, and other components to form structural components for electrical connections and signal detection. The collection line is an important component of the BMS (battery management system) for Electric Vehicles which is used to monitor the voltage and temperature of power battery cells. It can connect data collection and transmission and has an overcurrent protection function. When an abnormal short circuit occurs, it can automatically disconnect to protect the battery cell.
In BMS, the cost and space utilization of batteries are key issues. With the technological development of battery capacity reaching its limit, it is necessary to improve efficiency through structural design. Replacing traditional BMS wiring with flexible printed circuits can ensure stable performance. At present, the application of flexible printed circuits in electric vehicles mainly focuses on the battery, as the FPC for power battery market is expanding rapidly, driven by advancements in battery technology. Improving battery technology, reducing size, and lowering costs are critical objectives. CTP and CTC technologies improve system energy density by simplifying internal structural components and increasing battery pack volume utilization. If solid-state batteries can be mass-produced by 2025, battery technology will usher in rapid development.
The Shift from Copper Wiring to Flexible Printed Circuit in EV Assembly
Previously, the power battery collection line for new energy vehicles usually used traditional copper wire harness solutions, but when dealing with large amounts of current signals, copper wire harnesses would occupy a lot of space. During the pack assembly process, traditional wiring harnesses rely on fixing the ports onto the battery pack manually, resulting in a lower level of automation. In contrast, the flexible printed circuit has the characteristics of high integration, ultra-thin thickness, and ultra-softness, and has outstanding advantages in safety, portability, layout, and other aspects. The application of flexible PCB in soft-pack batteries and hard-pack batteries is different, and the practices of different manufacturers are also different, including different termination forms, such as crimping, welding, etc. The biggest advantage of a flexible printed circuit is its flexibility. With the upgrading of battery control technology, they can evolve into various forms, and they also can be customized. In addition, the flexible printed circuit has a thin thickness and the battery pack structure can be customized. During assembly, it can be grabbed by a robotic arm and placed directly on the battery pack. It has a high degree of automation and is suited for large-scale production. The trend of replacing copper wire harnesses with flexible printed circuits is very obvious.

Advantages of Flexible Printed Circuits in Power Battery Modules
Safety performance
While replacing the weak current wires, a flexible printed circuit uses metal plates to connect the busbar and adds a fuse protection current design to ensure high-speed information transmission routes. This ensures that even if there is a short circuit problem in the battery pack, the internal design of flexible printed circuit will directly fuse the copper wires of the circuit, avoiding combustion or explosion in other parts of the battery pack.
Lightweight
Compared with traditional wiring harnesses and Rigid PCB products used for signal acquisition, Flexible printed circuit occupies less space in the battery pack and have a lighter overall weight. When used in the entire vehicle, it can reduce approximately 1kg of weight compared to wire harness solutions.
Flexibility of the process
Compared with the traditional wiring harness with multiple insertion points and complex manual insertion processes, Flexible printed circuit breaks through the limitations of process selection. The product can be combined with the characteristics of the battery pack to select various processes such as ultrasonic and welding; It has advantages in thickness (0.34mm in the line area, 2mm at NTC) and flexibility (90 ° and 180 ° bending assembly can be achieved in the line area).
Automated production
Because of fast and precise assembly, it is conducive to achieving automation. In terms of assembly, it is possible to avoid many manual errors in wiring harness design and also reduce incorrect insertion at the connector level. Flexible circuit boards have a regular shape and higher design integration, which can save a lot of wiring and connection work. They are suitable for large-scale mechanical mass production, greatly reducing assembly time and saving labor while providing a foundation for the automation of the power battery assembly process. This has further driven the demand in the FPC for the power battery market, as flexible solutions become indispensable in modern power battery manufacturing.
In the era of smart vehicles, the extensive automation application of flexible circuit boards on batteries is the trend of future development. In the long run, with technological upgrades, many low-voltage wiring harness units in vehicles may be gradually replaced, especially in intelligent vehicles that require increasingly high signal anti-interference requirements. The circuits of the motherboard and slave board may even be replaced by chips, which can be installed on flexible circuit boards to improve product stability, save space, and reduce costs (although cost advantages have not yet been demonstrated). The process of technological iteration often involves improvements at a more fundamental level.